Screw Connection Market
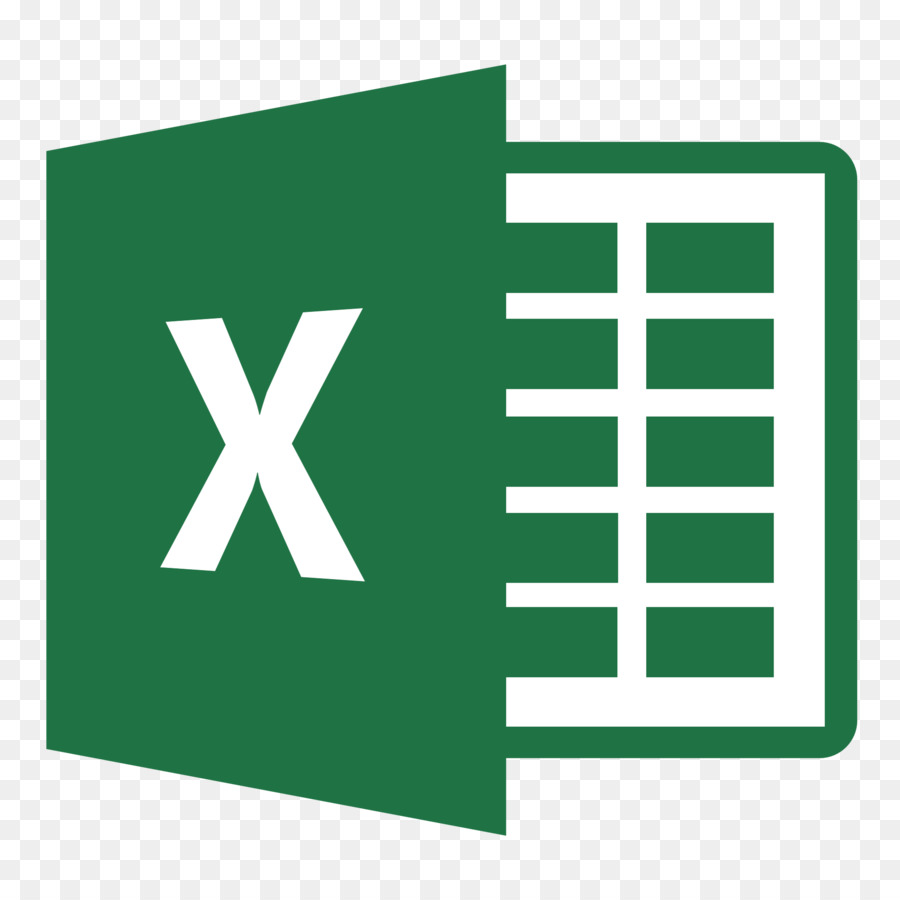
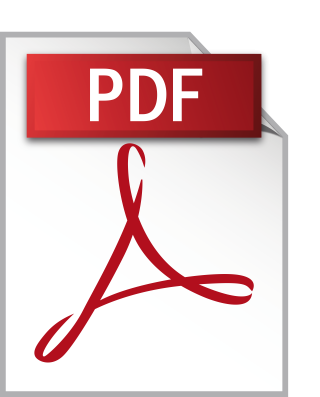
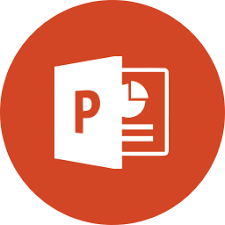
A screw connection is a mechanical fastening method that joins two or more components using a threaded screw. It provides a secure and adjustable connection, commonly used in construction, machinery, and electronics, ensuring stability and ease of assembly or disassembly.
The screw connection market is driven by the increasing demand for efficient and reliable fastening solutions across various industries, including automotive, aerospace, and construction. However, challenges such as the rising cost of raw materials, supply chain volatility, and the need for high-quality standards remain significant barriers. Despite these challenges, opportunities exist in developing eco-friendly fastening solutions and leveraging advancements in 3D printing and material technologies. Emerging sectors like electric vehicles and renewable energy also present avenues for innovation and growth within the market.
The global screw connection market is primarily driven by the increasing demand for fast and efficient assembly in a variety of industries, particularly automotive, construction, and electronics. As manufacturing processes become more automated, screws and screw connections are vital in ensuring that parts are securely fastened and remain durable over time. The rise of industrial automation has further spurred the need for standardized fastening solutions that ensure quick assembly and minimize human error.
Advancements in material science have also played a significant role in the market's growth. The development of stronger, more corrosion-resistant materials for screws and connectors has improved the longevity and reliability of connections, especially in harsh environments. These innovations have made screw connections a preferred choice in industries like aerospace, marine, and energy, where high-strength and long-lasting connections are critical.
The expansion of infrastructure projects, particularly in emerging economies, has further boosted the demand for screw connections. As construction projects grow in scale and complexity, the need for secure, cost-effective fastening solutions has become more important. Fastening systems, especially screws, are seen as essential components in the construction of bridges, roads, and buildings, contributing to the market's steady growth.
Shifting consumer preferences toward lightweight yet durable products also influence the market dynamics. The automotive industry, for example, is increasingly focusing on reducing vehicle weight for fuel efficiency while maintaining structural integrity. Screws made from advanced materials, like titanium or carbon fiber composites, are gaining popularity for this purpose. These materials provide the necessary strength without adding excessive weight, thereby supporting the ongoing demand for screw connections in various industries.
The global screw connection market faces significant challenges related to the increasing cost of raw materials and the volatility in supply chains. The prices of metals like steel, aluminum, and titanium, which are essential for manufacturing screws, fluctuate due to factors such as geopolitical tensions, trade policies, and disruptions in mining and production activities. This unpredictability can affect manufacturing costs, leading to price hikes for screws and connectors. Furthermore, the need for highly precise and high-quality components in industries such as aerospace and automotive has heightened the demand for advanced production technologies. However, these technologies often require substantial investments, adding to the overall cost burden for manufacturers. Manufacturers also face pressure to meet stringent quality control standards, which necessitates the use of expensive equipment and regular testing to ensure screw connections perform reliably under extreme conditions.
The global screw connection market presents key opportunities in the development of innovative fastening solutions that cater to emerging industries, particularly renewable energy and electric vehicles (EVs). With the increasing focus on sustainability, there is a growing demand for eco-friendly and energy-efficient components, creating a space for screws designed to reduce environmental impact. For example, screws that are lighter, more durable, and made from recyclable or sustainably sourced materials can appeal to industries striving to meet green certifications. In the electric vehicle sector, there is an opportunity to design specialized screw connections for EV batteries, motor assemblies, and lightweight frames, where traditional fasteners may not be optimal due to the unique requirements of these applications. Furthermore, as 3D printing technology evolves, the market can explore opportunities in producing customized screws and fasteners that meet the specific needs of highly specialized applications, opening new markets and creating differentiation for manufacturers who can innovate within this space.
Product Type
Stainless steel is a widely used material in the screw connection market due to its strength, corrosion resistance, and durability. This makes it ideal for applications in industries like automotive, aerospace, and construction, where longevity and resistance to harsh environments are essential. Stainless steel screws are often used in high-performance settings, such as marine environments and industrial machinery, where the material’s ability to withstand moisture, chemicals, and high temperatures is a key advantage.
Electrolytic steel screws are favored for their cost-effectiveness and enhanced surface quality. The electroplating process used in their production improves the appearance and durability of the steel, making it resistant to corrosion and wear. These screws are commonly employed in less extreme environments compared to stainless steel options but still serve effectively in industries such as automotive manufacturing and general construction. Electrolytic steel also allows for easier mass production, making it a popular choice for large-scale manufacturing.
Copper is used in screw connections where electrical conductivity is a primary requirement. Copper screws are particularly important in the electronics and electrical industries, where they facilitate the efficient transfer of electricity without resistance. These screws are essential in the assembly of electrical devices, such as circuit boards, and in the construction of power systems. Copper’s malleability also makes it ideal for applications that require precision, though it is typically used in less demanding mechanical environments due to its susceptibility to corrosion over time.
Copper alloy screws offer enhanced strength and resistance to corrosion compared to pure copper. The alloying process introduces other metals such as tin or zinc, which improve the material's overall performance, particularly in applications requiring both electrical conductivity and mechanical strength. Copper alloy screws are commonly found in industries like telecommunications, electronics, and automotive, where they are used in high-demand, durable applications. These screws combine the benefits of copper’s electrical properties with the added advantages of greater resilience and longer life expectancy in challenging conditions.
Application
Distribution box applications in the screw connection market are crucial for ensuring the secure and reliable connection of electrical components. Screws are used to fasten terminals, wiring, and other essential parts within distribution boxes, which are pivotal in managing the flow of electricity in residential, commercial, and industrial settings. The screws in distribution boxes need to offer excellent conductivity and strong mechanical strength to maintain safety and functionality in electrical systems.
Electric motor applications rely on screw connections to secure components such as stators, rotors, and other mechanical elements within the motor. The screws must provide high precision and durability to withstand the vibrations and high-speed rotations typical in electric motors. This makes screw connections in electric motors critical for maintaining the operational efficiency and longevity of the motor, especially in industrial and automotive sectors where electric motors are used extensively.
Automotive electrical systems use screw connections to assemble key components like battery terminals, lighting, wiring harnesses, and control units. These screws must meet specific requirements for electrical conductivity and resistance to corrosion, ensuring reliable connections in vehicles. The automotive industry often requires screws that can withstand high temperatures, vibrations, and environmental conditions, making the quality of screw connections essential for the safety and performance of modern vehicles.
TV set applications make use of screw connections to assemble and secure various internal components, such as the screen, circuit boards, and power supply units. The screws ensure that the parts are firmly in place and that the device operates effectively without malfunction due to loose or unstable connections. Given the compact nature of modern television sets, screws used in these applications need to be small yet strong, offering both mechanical stability and resistance to wear.
Other applications in the screw connection market cover a wide range of industries, from telecommunications to consumer electronics. These include the use of screws in devices like computers, medical equipment, and industrial machinery, where screws are needed to hold together various components that require high precision and strength. Screws in these applications are designed to meet the specific needs of each device, offering solutions for secure, long-lasting connections in diverse environments.
In North America, the screw connection market is driven by the robust automotive, aerospace, and construction industries. The region is characterized by high demand for precision-engineered fasteners, particularly in advanced manufacturing sectors. The automotive industry’s push toward lightweight and fuel-efficient vehicles increases the need for advanced screw connections made from materials like aluminum and titanium. Furthermore, the strong presence of aerospace companies in the U.S. and Canada boosts the market for high-strength, durable screw solutions capable of withstanding extreme conditions.
Europe, being home to some of the world’s leading automotive and machinery manufacturing hubs, has a significant demand for screw connections. The region’s focus on sustainability and green manufacturing also plays a pivotal role, as industries seek eco-friendly fastening solutions. Countries like Germany and France, with their strong engineering and automotive sectors, drive innovation in screw technologies. Additionally, Europe’s leadership in renewable energy projects, particularly wind energy, creates a growing market for specialized screw connections in the energy sector.
Asia Pacific holds the largest share of the global screw connection market, with China, Japan, and India leading the way in manufacturing and construction industries. The region benefits from rapid industrialization, increased infrastructure development, and expanding automotive production. China’s dominance in manufacturing, coupled with its heavy investments in infrastructure, has significantly boosted the demand for screw connections. Japan’s advanced automotive and electronics sectors also contribute to this growth, while India’s expanding construction and manufacturing sectors continue to drive demand for fasteners.
In Latin America, the screw connection market is experiencing steady growth due to increasing infrastructure development, particularly in Brazil and Mexico. These countries are investing heavily in roadways, buildings, and industrial infrastructure, which require reliable and cost-effective fastening solutions. The automotive sector in Mexico also plays a role, as it is a significant manufacturing base for North American and global automotive brands. While the market is still growing, Latin America represents an emerging opportunity as industries modernize and expand.
The Middle East and Africa region presents mixed opportunities in the screw connection market. The Middle East, particularly countries like Saudi Arabia and the UAE, is seeing growth due to large-scale infrastructure projects, such as the development of new cities and expansion of the energy sector. The oil and gas industry, which demands high-performance screws for equipment in extreme environments, significantly contributes to the market. In contrast, the African market is growing more slowly due to lower levels of industrialization and infrastructure development but is expected to expand as more investments are made in energy, mining, and construction projects.