Reaction Curing Coating Market
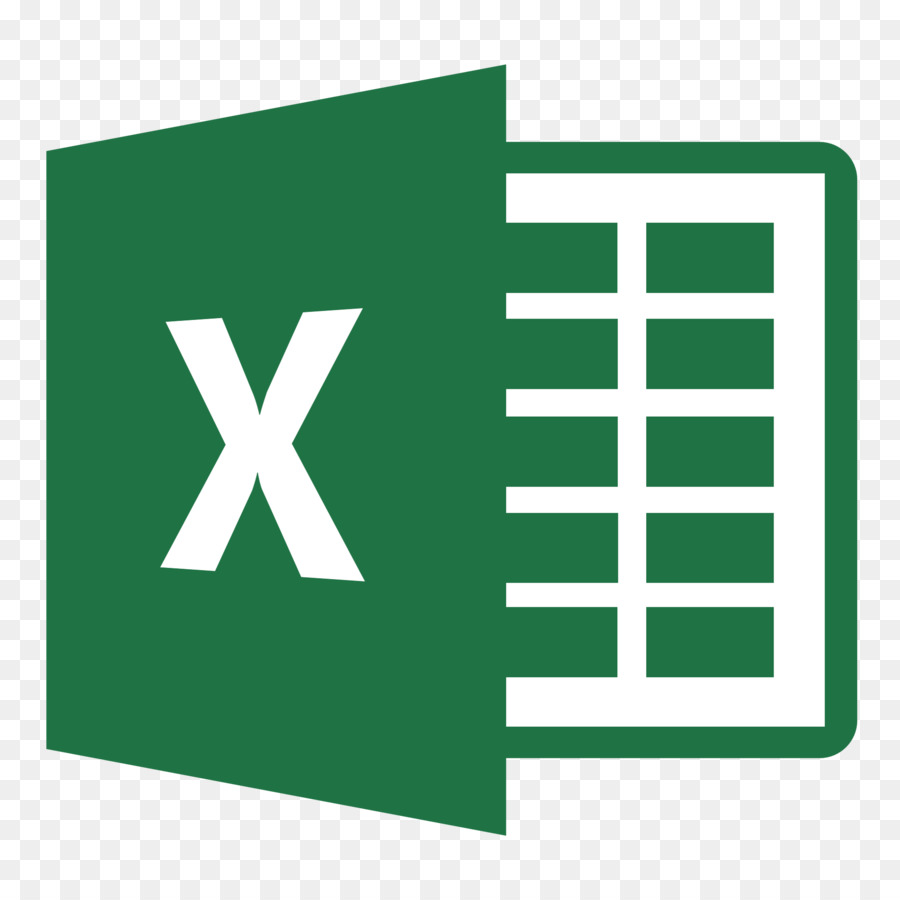
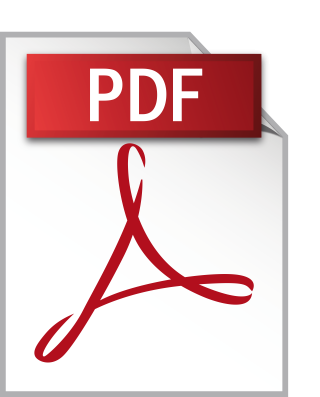
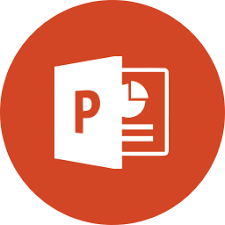
Reaction curing coating is a type of coating that hardens through a chemical reaction, such as polymerization or cross-linking, triggered by heat, light, or a curing agent. It forms a durable, protective layer with strong adhesion, commonly used in electronics, automotive, and industrial applications.
The reaction curing coating market is driven by increasing demand from industries like automotive, aerospace, electronics, and construction due to its durability and high-performance properties. Challenges include high production costs, complex application processes, and regulatory compliance, which may limit adoption. Opportunities arise from advancements in nanotechnology, development of eco-friendly coatings, and growing demand for specialized formulations in emerging industries such as healthcare and renewable energy.
The driving factors of the global reaction curing coating market stem from its diverse applications across industries and the growing demand for high-performance coatings. One primary factor is the increased adoption in the automotive and aerospace industries due to the need for durable, lightweight, and corrosion-resistant coatings. These industries require advanced materials to enhance the longevity and performance of vehicles and aircraft, making reaction curing coatings an ideal choice.
The rapid growth of the electronics industry also significantly drives the market. Reaction curing coatings provide excellent insulation, moisture resistance, and thermal stability, making them essential for protecting sensitive electronic components. With the rising demand for consumer electronics, smart devices, and renewable energy systems, the use of these coatings is expanding globally.
Another important factor is the stringent environmental regulations encouraging the adoption of eco-friendly coatings. Reaction curing coatings, particularly those that are solvent-free or low in volatile organic compounds (VOCs), align with global sustainability goals. This trend has spurred innovation, with manufacturers investing in research to develop environmentally friendly products that meet regulatory requirements.
The construction sector also plays a vital role in market growth, driven by the demand for protective coatings that enhance structural durability. Reaction curing coatings are widely used for their chemical resistance, abrasion protection, and weatherproofing properties, making them suitable for infrastructure projects and industrial facilities in varying environmental conditions.
The global reaction curing coating market faces challenges related to the high cost of raw materials and production processes, which can limit accessibility for cost-sensitive industries. The complexity of application and curing processes often requires specialized equipment and skilled labor, which may deter smaller businesses from adopting these coatings. Regulatory compliance adds another layer of difficulty, as manufacturers must adhere to strict environmental standards, especially concerning volatile organic compounds (VOCs) in some formulations. Market growth is also hindered by competition from alternative coatings, such as waterborne and powder coatings, which are perceived as simpler and more cost-effective in certain applications. Economic fluctuations and supply chain disruptions further impact the availability and pricing of key raw materials, creating uncertainty for market participants.
The global reaction curing coating market offers significant opportunities through advancements in nanotechnology and material science, enabling the development of next-generation coatings with enhanced properties such as self-healing, anti-microbial, and improved UV resistance. These innovations cater to high-tech industries like healthcare, electronics, and renewable energy, which demand specialized coatings for unique applications. Emerging markets in Asia-Pacific, Latin America, and Africa present untapped potential due to rapid industrialization and urbanization, creating a need for advanced coatings in construction, infrastructure, and manufacturing sectors. Collaborative efforts between research institutions and industry players to develop sustainable, bio-based formulations provide an avenue for differentiation and long-term growth, aligning with global sustainability goals and customer preferences for greener products.
Product Type
The one-component coating segment in the reaction curing coating market is characterized by its ease of application and convenience, as it does not require mixing before use. These coatings are pre-formulated with all necessary components, making them ideal for applications where consistency and quick application are critical. They are widely used in industries like electronics and automotive, where their single-step curing process saves time and reduces labor costs.
The two-component coating segment is known for its superior performance and durability, as it involves mixing a resin and a hardener just before application. This allows for greater control over curing properties and enhances the mechanical strength and chemical resistance of the coating. Two-component coatings are extensively utilized in demanding environments such as industrial equipment, marine structures, and heavy-duty applications where long-term protection is essential.
Application
The building segment in the reaction curing coating market benefits from its ability to provide protection against harsh environmental conditions, corrosion, and wear. These coatings are widely used for infrastructure projects, including bridges, pipelines, and commercial buildings, offering long-lasting durability and aesthetic appeal.
The automobile segment drives demand for reaction curing coatings due to the need for lightweight, corrosion-resistant, and durable materials. These coatings enhance vehicle performance and longevity by protecting surfaces from wear and environmental exposure, while also contributing to advanced designs and finishes.
The mechanical segment relies on reaction curing coatings for machinery and industrial equipment to provide resistance against extreme temperatures, abrasion, and chemical exposure. These coatings are critical in extending the operational life of heavy machinery and ensuring efficient performance in demanding industrial applications.
The wood and furniture segment uses reaction curing coatings to enhance the appearance, durability, and resistance of wooden surfaces against moisture, heat, and scratches. These coatings are essential for high-quality finishes in furniture manufacturing and interior décor, offering both protection and aesthetic value.
The aerospace segment extensively uses reaction curing coatings for aircraft components due to their ability to withstand high stress, temperature fluctuations, and environmental conditions. These coatings ensure safety, reliability, and reduced maintenance costs for aerospace equipment and structures.
The others segment includes diverse applications such as electronics, marine, and renewable energy industries, where reaction curing coatings provide tailored solutions for specific needs like electrical insulation, UV protection, and corrosion resistance in challenging environments.
The reaction curing coating market in North America is driven by robust demand from industries such as automotive, aerospace, and electronics. The region benefits from advanced manufacturing technologies and stringent environmental regulations, pushing companies to adopt high-performance, low-VOC coatings. The U.S. dominates the market due to its strong industrial base and ongoing R&D efforts in innovative coating solutions.
In Europe, the market is supported by the automotive and construction sectors, with countries like Germany, France, and the UK leading in demand. Strict EU regulations regarding environmental sustainability have accelerated the adoption of eco-friendly reaction curing coatings. The region also sees significant growth in protective coatings for renewable energy infrastructure, such as wind turbines.
The Asia Pacific region represents the fastest-growing market, fueled by rapid industrialization and urbanization in countries like China, India, and Japan. The expansion of the electronics, automotive, and construction sectors in this region has created a substantial need for advanced coatings. Low manufacturing costs and increasing foreign investments further contribute to the region's growth.
In Latin America, the market growth is moderate, driven by the construction and oil & gas industries. Brazil and Mexico are the key contributors, where infrastructure development and industrial activities generate demand for protective coatings. However, economic instability in certain areas may pose challenges to sustained growth.
The Middle East & Africa market is primarily driven by the oil & gas and construction industries. Countries like Saudi Arabia, the UAE, and South Africa are key markets due to ongoing infrastructure projects and industrial expansion. The harsh environmental conditions in the region, such as high temperatures and sand exposure, create a strong need for durable and weather-resistant coatings.