Metallographic Polishing Machine Market
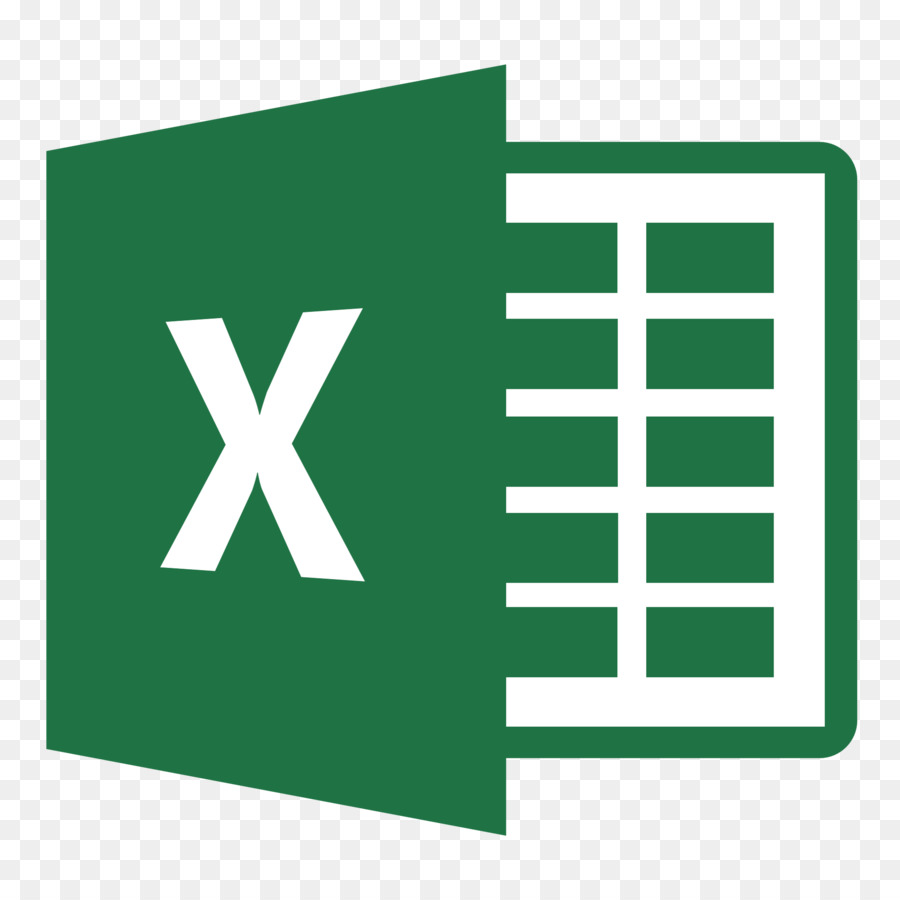
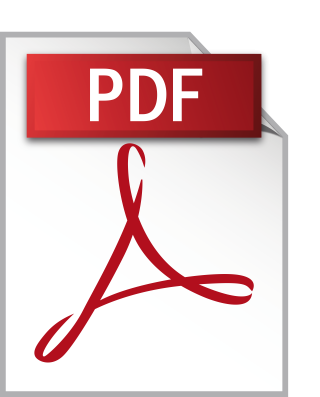
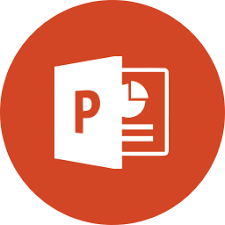
A metallographic polishing machine is a specialized equipment used to prepare metal and alloy samples for microscopic analysis by creating a smooth and reflective surface. It removes surface irregularities, scratches, and deformation layers through controlled grinding and polishing processes using abrasive materials. This machine is essential in material science, quality control, and research to study the microstructure and properties of metals with high precision.
The metallographic polishing machine market is driven by the rising demand for precise material analysis in industries like automotive, aerospace, and electronics, along with advancements in additive manufacturing and laboratory automation. Challenges include high equipment costs, the need for skilled operators, and strict quality regulations in material testing. Opportunities arise from the growing adoption of AI-driven polishing systems, increasing semiconductor manufacturing, and expanding applications in renewable energy, medical devices, and advanced materials research. The shift toward automated, high-precision polishing solutions is expected to shape market growth.
The increasing demand for precise material analysis in industrial and research applications is driving the metallographic polishing machine market. Metallography is essential for studying the microstructure of metals, alloys, ceramics, and composites, making polishing machines a critical tool in laboratories and manufacturing facilities. Industries such as automotive, aerospace, and electronics rely on metallographic analysis to ensure product quality, material durability, and performance reliability. As advanced materials continue to emerge, the need for high-precision polishing solutions grows, supporting the adoption of automated and semi-automated metallographic polishing machines in quality control and R&D laboratories.
The expansion of the automotive and aerospace industries is significantly influencing the demand for metallographic polishing machines. These industries require high-strength materials that undergo strict quality inspections to meet safety and performance standards. Metallographic analysis helps in detecting defects, measuring grain structures, and evaluating surface properties of metal components used in engines, turbines, and structural parts. As manufacturers invest in lightweight alloys and high-performance materials to enhance fuel efficiency and reduce emissions, the need for accurate metallographic preparation methods increases. The growing use of electric vehicles and advanced aerospace technologies further amplifies the demand for metallographic testing, strengthening the market for polishing machines.
The rise of additive manufacturing and advanced manufacturing processes is boosting the demand for metallographic polishing machines. 3D-printed metal parts, composite materials, and precision-engineered components require detailed microstructural evaluation to assess their mechanical properties and ensure consistency. Industries such as medical devices, defense, and energy rely on metallographic analysis to validate the integrity of their materials, making efficient polishing solutions essential. The continuous advancements in metal fabrication techniques, including powder metallurgy and laser sintering, require high-quality sample preparation for microscopic examination, further supporting the adoption of metallographic polishing machines.
The growth of educational and research institutions focused on materials science and metallurgy is contributing to the expansion of the metallographic polishing machine market. Universities, technical institutes, and research laboratories invest in metallographic equipment to support academic programs, scientific studies, and industrial collaborations. The increasing number of research projects on nanomaterials, biomaterials, and high-performance alloys requires state-of-the-art polishing machines for accurate sample preparation. Governments and private organizations are funding material science research to drive innovations in energy, infrastructure, and healthcare, leading to greater demand for metallographic polishing equipment in academic and commercial laboratories.
The increasing emphasis on automation and digitalization in laboratory processes is accelerating the adoption of advanced metallographic polishing machines. Automated polishing machines improve consistency, reduce human error, and enhance productivity in high-throughput testing environments. Smart technologies, such as programmable polishing parameters, digital interfaces, and AI-driven optimization, are transforming material analysis workflows. Laboratories and industrial testing facilities are shifting toward automated solutions to streamline operations, improve repeatability, and meet stringent quality standards. The integration of digital imaging and data management systems with polishing machines is further enhancing efficiency, making modern metallographic equipment an integral part of material testing and inspection processes.
The metallographic polishing machine market faces challenges related to high initial costs and maintenance expenses, which limit adoption, especially among small-scale laboratories and manufacturers. Advanced models with automated features require significant investment, making affordability a concern for institutions with budget constraints. The complexity of operation and the need for skilled technicians add another layer of difficulty, as improper handling can lead to inconsistent results and increased material wastage. Strict regulatory standards in industries such as aerospace, automotive, and medical devices demand precise sample preparation, requiring manufacturers to develop high-precision machines that meet evolving industry requirements. Supply chain disruptions and fluctuations in raw material prices impact production costs, affecting the availability of critical machine components. The rising preference for outsourcing metallographic testing services also affects machine sales, as many companies opt for third-party testing rather than investing in in-house equipment. Rapid technological advancements require continuous innovation, making it challenging for manufacturers to keep up with evolving customer demands while maintaining cost-effectiveness. Environmental concerns related to waste disposal from polishing materials and the use of chemicals in the process create additional regulatory hurdles, pushing companies to develop more sustainable solutions.
The increasing adoption of automated and AI-driven metallographic polishing machines presents a major opportunity for market growth. Laboratories and industrial facilities are seeking advanced solutions that improve efficiency, reduce labor costs, and enhance precision in material analysis. Automated polishing systems with programmable controls and real-time monitoring capabilities offer consistent results, minimizing variability caused by manual operations. AI-powered machines can optimize polishing parameters based on material type and sample characteristics, reducing the need for skilled technicians. Companies investing in smart polishing equipment with remote operation, integrated imaging, and cloud-based data management can cater to the growing demand for high-throughput and error-free material preparation solutions.
The expansion of semiconductor and electronics manufacturing is creating new opportunities for metallographic polishing machine suppliers. As microelectronics and advanced semiconductor devices become smaller and more complex, precise material analysis is required to ensure product reliability and performance. The development of high-performance chips, flexible electronics, and 5G components relies on microstructural evaluation at the nanoscale level, increasing the need for high-precision polishing equipment. Manufacturers focusing on polishing machines with ultra-fine control, contamination-free operation, and compatibility with fragile semiconductor materials can gain a competitive edge in this rapidly evolving industry.
The rising investments in renewable energy and sustainable infrastructure are opening new applications for metallographic polishing machines. Wind turbines, solar panels, and energy storage systems require advanced materials that undergo strict quality testing to enhance efficiency and durability. Metallographic analysis plays a crucial role in evaluating weld integrity, fatigue resistance, and coating performance of materials used in clean energy projects. Companies that develop polishing machines optimized for composite materials, corrosion-resistant alloys, and energy-efficient coatings can benefit from the growing demand in the renewable energy sector. Governments and private organizations funding green energy initiatives are further driving the need for high-quality metallographic testing solutions.
The increasing demand for specialized metallographic solutions in the medical and biotechnology industries offers significant growth potential. Medical implants, prosthetics, and surgical instruments require precise material analysis to ensure biocompatibility, strength, and long-term performance. The use of advanced alloys, ceramics, and biomaterials in medical devices necessitates high-quality polishing to prepare samples for microstructural evaluation. As healthcare regulations become stricter, manufacturers must adhere to rigorous quality standards, increasing the need for reliable metallographic testing equipment. Companies that provide polishing machines designed for delicate medical-grade materials and contamination-free sample preparation can capitalize on the expanding healthcare and biomedical research sectors.
The growing interest in nanotechnology and advanced materials research is driving demand for high-precision metallographic polishing machines. Researchers developing next-generation materials for aerospace, defense, and quantum computing require ultra-fine polishing techniques to analyze material structures at the atomic level. Innovations in carbon-based materials, high-entropy alloys, and superconductor research are creating new challenges in sample preparation, requiring specialized polishing machines with sub-micron accuracy. Equipment manufacturers focusing on ultra-precision polishing systems, adaptive polishing techniques, and compatibility with emerging materials can tap into the expanding market of high-tech research institutions and advanced material laboratories.
Product Type
Automatic metallographic polishing machines are widely used in industries that require high-precision sample preparation with minimal manual intervention. These machines offer consistent polishing results, improving efficiency and reducing human errors. Advanced models come with programmable settings, enabling users to control parameters such as speed, pressure, and polishing time for different materials. The demand for these machines is rising in industries such as automotive, aerospace, and electronics, where strict quality control is essential. Automation helps reduce labor costs and increases throughput, making it a preferred choice for large-scale manufacturing and research facilities. This segment dominates the market due to its advantages in productivity, precision, and repeatability.
Manual metallographic polishing machines are commonly used in laboratories, educational institutions, and small-scale industries where lower sample volumes and cost considerations are key factors. These machines require skilled operators to achieve the desired surface finish, making them suitable for applications that do not demand high automation. They are widely used in metallurgical research, failure analysis, and academic training due to their affordability and flexibility. The market for manual machines remains steady, especially in regions where cost-sensitive buyers prefer lower initial investment over automation. While these machines provide control over the polishing process, they are gradually being replaced by automated solutions in industries that require high-volume sample preparation with consistent results.
Application
The use of metallographic polishing machines in industrial production is essential for ensuring material quality and performance in manufacturing processes. Industries such as automotive, aerospace, electronics, and energy rely on metallographic analysis to evaluate the microstructure of metals, composites, and coatings used in critical components. These machines help detect defects, verify material properties, and improve product reliability, making them a crucial part of quality control systems. With the increasing adoption of high-performance materials and precision engineering, manufacturers are investing in automated polishing solutions to enhance efficiency, reduce human error, and meet strict industry standards. The demand for durable and lightweight materials in industrial applications further drives the need for metallographic polishing machines in large-scale production environments.
The laboratory segment relies on metallographic polishing machines for research, material testing, and academic studies. Universities, government research institutions, and private laboratories use these machines to prepare samples for microstructural analysis, failure investigations, and new material development. Scientists and engineers working on advanced alloys, nanomaterials, and biomaterials require high-precision polishing equipment to achieve accurate results in microscopy and spectroscopy studies. As research in materials science continues to expand, laboratories seek polishing machines with enhanced automation, digital integration, and compatibility with a wide range of materials. The growing focus on sustainable materials and next-generation manufacturing technologies further increases the importance of metallographic polishing in research and innovation.
North America is a key market for metallographic polishing machines, driven by strong demand from industries such as aerospace, automotive, and medical devices. The presence of advanced research institutions and material testing laboratories supports the adoption of high-precision polishing equipment. Strict quality control regulations in manufacturing sectors create a need for reliable sample preparation solutions, encouraging investment in automated machines. High labor costs push companies to adopt automated polishing systems to improve efficiency and reduce operational expenses. However, market growth is affected by budget constraints in small and mid-sized laboratories, limiting the adoption of advanced equipment. Leading manufacturers focus on technological innovations to enhance machine performance and meet evolving industry requirements.
Europe has a well-established metallographic polishing machine market, supported by strong industrial and research infrastructure. The automotive and aerospace sectors play a major role in driving demand for high-precision sample preparation solutions. Stringent regulations on material testing and quality assurance require advanced metallographic analysis, increasing the demand for high-end polishing machines. The presence of leading machine manufacturers ensures continuous innovation and product development, improving market competitiveness. Economic uncertainties and fluctuations in industrial production affect capital investments in new equipment, creating challenges for manufacturers. Sustainability initiatives drive the development of eco-friendly polishing solutions, pushing companies to adopt water-based and low-waste polishing processes.
Asia Pacific is the fastest-growing region in the metallographic polishing machine market, fueled by rapid industrialization and expanding manufacturing activities. Countries such as China, Japan, and South Korea have strong automotive, electronics, and metal fabrication industries, creating high demand for metallographic sample preparation. The increasing focus on material quality and process optimization in industrial production drives the need for advanced polishing machines. Government investments in research and development, especially in semiconductor and materials science, boost market growth. The presence of low-cost manufacturers intensifies competition, leading to price pressures on high-end machines. Rising labor costs in some countries encourage the adoption of automated systems, while small-scale manufacturers continue to rely on manual polishing solutions due to cost constraints.
Latin America experiences steady growth in the metallographic polishing machine market, supported by developments in the mining, metallurgy, and automotive industries. Brazil and Mexico lead the market due to their strong industrial bases and growing research sectors. Increasing demand for quality control in manufacturing drives the adoption of metallographic testing equipment, although budget limitations in small enterprises restrict market expansion. Limited local production of advanced polishing machines increases dependence on imports, making the market vulnerable to price fluctuations and supply chain disruptions. Efforts to modernize industrial processes and improve material testing standards contribute to gradual market growth, with an increasing focus on automation to enhance efficiency.
The Middle East & Africa market for metallographic polishing machines is developing at a slower pace due to limited industrial and research infrastructure. The oil and gas, mining, and construction industries contribute to demand for material testing equipment, but investment in advanced polishing machines remains low compared to other regions. Research institutions and universities play a small but growing role in driving demand, as governments invest in science and technology to diversify their economies. Import dependency and high equipment costs challenge market expansion, making affordability a key concern for buyers. The increasing presence of international manufacturers and distributors improves market accessibility, while local industries gradually adopt modern material testing methods to improve product quality and compliance with global standards.