Metallographic Hardness Tester Market
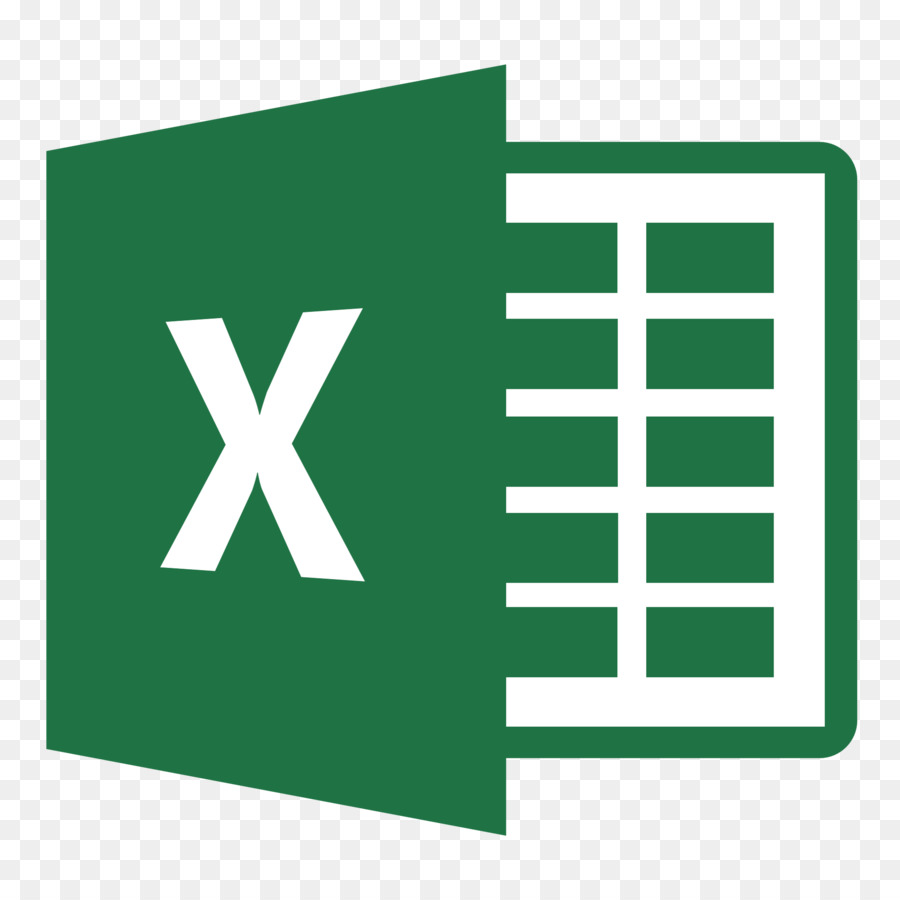
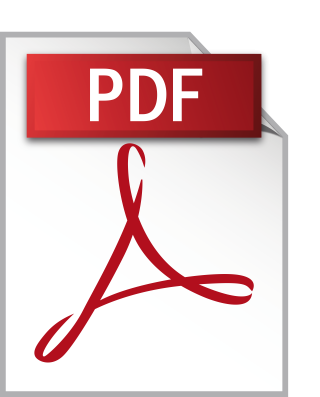
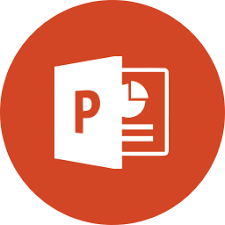
A metallographic hardness tester is a device used to measure the hardness of metals and alloys by assessing their resistance to deformation under a specific force. It determines material properties such as strength, wear resistance, and durability by indenting the surface with a standardized probe. These testers are essential in quality control, research, and manufacturing to ensure material reliability and performance.
The metallographic hardness tester market is driven by the growing need for quality control in manufacturing, increasing adoption of automation, and rising investments in material research. Challenges include high equipment costs, the complexity of advanced testing methods, and the need for skilled operators. Opportunities exist in AI-powered testing systems, digital integration for real-time analysis, and expanding applications in infrastructure and high-performance material development. The demand for precise and efficient hardness testing solutions is expected to grow as industries focus on improving material reliability and regulatory compliance.
The increasing demand for quality control in manufacturing industries is driving the metallographic hardness tester market. Industries such as automotive, aerospace, and metal fabrication require precise hardness testing to ensure material strength, durability, and compliance with industry standards. Hardness testing is essential in assessing the mechanical properties of metals, alloys, and composites used in structural and safety-critical components. As manufacturers focus on improving product reliability and performance, the adoption of advanced hardness testers is rising. The need to maintain consistency in material quality across production batches is encouraging industries to invest in modern hardness testing solutions with higher accuracy and automation.
The growing adoption of automation and digitalization in material testing is contributing to market expansion. Traditional hardness testing methods are being replaced by automated and computer-controlled systems that provide faster results, higher precision, and improved repeatability. Automated hardness testers integrated with software solutions allow for real-time data analysis, remote monitoring, and seamless reporting. These features are particularly beneficial for large-scale manufacturing and research laboratories that require continuous testing and high throughput. The increasing use of artificial intelligence and machine learning in material testing processes is also enhancing the efficiency of metallographic hardness testers by reducing human errors and improving test standardization.
The rising focus on material research and development in industries such as electronics, medical devices, and defense is boosting demand for advanced hardness testing equipment. New materials, including lightweight alloys, high-strength composites, and nanomaterials, require specialized testing methods to evaluate their mechanical properties. Research institutions and material testing laboratories are investing in advanced hardness testers with micro and nano-indentation capabilities to analyze material behavior at different scales. As the development of high-performance materials becomes more critical for various applications, the demand for sophisticated hardness testing instruments is increasing to support innovation and ensure material reliability.
The expansion of infrastructure and construction projects is driving demand for metallographic hardness testers in the steel, cement, and heavy equipment industries. Structural materials used in bridges, buildings, and transportation systems must undergo rigorous hardness testing to meet safety regulations and durability standards. Construction companies and material suppliers are adopting advanced testing technologies to evaluate the hardness and wear resistance of materials exposed to harsh environmental conditions. The increasing adoption of hardened steel, reinforced concrete, and composite materials in modern infrastructure projects is further supporting the demand for reliable and efficient hardness testing solutions.
The rising emphasis on regulatory compliance and safety standards in various industries is pushing companies to invest in high-precision hardness testing equipment. Industries such as oil and gas, power generation, and manufacturing are required to follow strict material testing guidelines to prevent structural failures and operational risks. Hardness testing plays a critical role in ensuring that components such as pipelines, pressure vessels, and machinery parts meet safety and performance requirements. As regulatory bodies continue to enforce stringent quality control measures, manufacturers and testing laboratories are increasingly relying on metallographic hardness testers to ensure compliance and avoid costly failures.
The metallographic hardness tester market faces challenges due to the high initial cost of advanced testing equipment, which limits adoption among small and medium-sized enterprises. The need for precise calibration and regular maintenance increases operational costs, making it difficult for some users to sustain long-term usage. Technological advancements require continuous upgrades, which can lead to compatibility issues with existing systems and additional training requirements for operators. The market is also influenced by strict industry standards and regulations that demand frequent modifications in testing methods, adding to compliance costs. Supply chain disruptions and fluctuations in raw material prices impact production, affecting the availability and affordability of these testers. Competition among manufacturers leads to price pressure, reducing profit margins and limiting investment in research and development for innovative solutions. Economic downturns and budget constraints in industries such as automotive and aerospace affect the demand for hardness testers, further hindering market growth.
The increasing adoption of automated and AI-powered hardness testing systems presents a significant opportunity for the metallographic hardness tester market. Industries are shifting toward automated solutions that reduce human errors, enhance precision, and provide real-time data analysis. Advanced systems with AI integration can optimize testing procedures, identify patterns in material properties, and improve predictive maintenance strategies. This trend is particularly beneficial for large-scale manufacturing and research applications where efficiency and accuracy are critical. As industries continue to embrace smart manufacturing and digital transformation, the demand for intelligent hardness testers with data connectivity and remote monitoring capabilities is expected to rise.
Product Type
Vicker hardness tester is widely used for measuring the hardness of thin materials, small parts, and coatings. It uses a diamond pyramid-shaped indenter to create an indentation under a specific load, and the size of the indentation determines the material’s hardness. This segment is commonly adopted in laboratories, research institutions, and precision manufacturing industries due to its high accuracy and ability to measure small areas. The demand for vicker hardness tester is growing in industries such as electronics, aerospace, and medical devices, where precise material testing is essential.
Rockwell hardness tester is one of the most commonly used hardness testing methods in industrial applications. It measures hardness by applying a fixed load using a steel or tungsten carbide ball or a conical diamond indenter and then assessing the depth of penetration. This segment is dominant in the metallographic hardness tester market due to its fast and straightforward testing process, making it ideal for production lines, automotive manufacturing, and metalworking industries. Its ability to test a wide range of materials, including metals, plastics, and composites, contributes to its strong market presence.
Brinell hardness tester is mainly used for testing materials with coarse microstructures or rough surfaces, such as castings and forgings. It utilizes a hardened steel or tungsten carbide ball to create an indentation under a heavy load, and the diameter of the indentation determines the material’s hardness. This segment is commonly applied in heavy industries such as construction, shipbuilding, and mining, where large metal components require hardness evaluation. The demand for brinell hardness tester remains stable due to its effectiveness in testing materials that are too rough or uneven for other hardness testing methods.
Universal hardness tester is gaining popularity as a versatile solution capable of performing multiple hardness testing methods, including vicker, rockwell, and brinell. It provides flexibility for industries that require various hardness measurements within a single system, reducing the need for multiple testers. The ability to switch between different testing methods makes this segment the fastest-growing in the metallographic hardness tester market, especially in research and development, high-precision manufacturing, and academic institutions. The increasing focus on multifunctional testing equipment drives its adoption among manufacturers seeking efficiency and cost-effectiveness.
Others category includes specialized and emerging hardness testing methods that do not fit into the main segments. This includes knoop hardness testers, microhardness testers, and automated digital hardness testers designed for specific applications. These solutions are often used in niche industries such as nanotechnology, semiconductor manufacturing, and advanced material research. As technological advancements continue, the demand for automated and digital hardness testing solutions is expected to rise, offering improved accuracy, efficiency, and data integration capabilities.
Application
Industrial production relies on metallographic hardness testers to ensure the durability and strength of materials used in manufacturing processes. Hardness testing is essential in industries such as automotive, aerospace, metal fabrication, and heavy machinery to verify material properties before they are used in critical components. Manufacturers use these testers to assess the wear resistance of metals, alloys, and coatings to prevent product failures and maintain quality standards. Automated hardness testers are increasingly adopted in production lines to improve efficiency, reduce human errors, and support high-volume testing. As industries focus on enhancing product reliability and regulatory compliance, the demand for hardness testing equipment in industrial production continues to grow.
Laboratory applications of metallographic hardness testers focus on material research, quality assurance, and failure analysis across various industries. Research institutions, universities, and independent testing labs use these testers to study the mechanical properties of new materials, including high-strength alloys, composites, and nanomaterials. Laboratories require precise and advanced hardness testing methods, such as micro and nano-indentation, to analyze materials at microscopic levels. These tests help in understanding material behavior, developing innovative products, and improving manufacturing processes. As industries continue to explore new materials for advanced applications, laboratories play a crucial role in providing reliable hardness data, increasing the need for high-precision metallographic hardness testers.
North America has a strong demand for metallographic hardness testers due to the presence of advanced manufacturing industries, including aerospace, automotive, and defense. The region’s focus on quality control and compliance with strict industrial standards drives the adoption of high-precision testing equipment. The market benefits from technological advancements, with manufacturers investing in automation and digitalization to improve efficiency and accuracy. The high cost of sophisticated hardness testers poses a challenge for small-scale industries, while economic uncertainties and fluctuations in manufacturing activities influence market growth. The competitive landscape includes both global and regional players, with research institutions and industrial laboratories continuously seeking improved testing solutions.
Europe sees steady growth in the metallographic hardness tester market, driven by its well-established automotive, machinery, and metalworking industries. Stringent regulations regarding product quality and safety encourage companies to adopt advanced testing equipment. Investments in research and development support innovation in hardness testing technology, with an increasing shift toward automated and digital solutions. The market faces challenges related to high equipment costs and the need for skilled professionals to operate sophisticated testing systems. The presence of multiple established manufacturers results in intense competition, leading to product differentiation strategies and continuous advancements in testing capabilities. Economic fluctuations and supply chain issues also impact the demand for hardness testers across industries.
Asia Pacific is the fastest-growing market for metallographic hardness testers, fueled by rapid industrialization, expansion of manufacturing sectors, and rising investments in quality control. Countries such as China, Japan, and South Korea lead the market due to their strong presence in automotive, electronics, and heavy machinery industries. The region benefits from government initiatives supporting industrial growth and research activities. The increasing demand for automated testing solutions is reshaping the competitive landscape, with both international and domestic manufacturers expanding their product offerings. Price sensitivity remains a challenge, as many small and mid-sized enterprises seek cost-effective solutions. Supply chain disruptions and fluctuating raw material prices also impact market stability.
Latin America experiences moderate growth in the metallographic hardness tester market, supported by the expansion of metalworking, mining, and construction industries. Countries such as Brazil and Mexico drive demand due to their growing manufacturing capabilities and investments in industrial infrastructure. The market faces challenges related to limited access to advanced testing equipment, as high costs and economic instability affect procurement decisions. The presence of global manufacturers and the increasing awareness of quality control standards are gradually improving adoption rates. Government initiatives aimed at strengthening industrial production provide opportunities for market growth, though reliance on imports and fluctuations in currency exchange rates create uncertainties for businesses.
The Middle East & Africa has a developing market for metallographic hardness testers, primarily driven by the oil and gas, construction, and metal industries. Infrastructure development and investments in industrial production contribute to market expansion, with growing demand for reliable testing solutions. Limited local manufacturing and dependence on imported equipment pose challenges, as high costs and logistical barriers impact adoption. The competitive landscape is shaped by global suppliers partnering with regional distributors to enhance market penetration. Increasing awareness of material quality standards and advancements in industrial research are expected to drive future demand for hardness testing equipment in this region.