Metallographic Cold Mounting Consumables Market
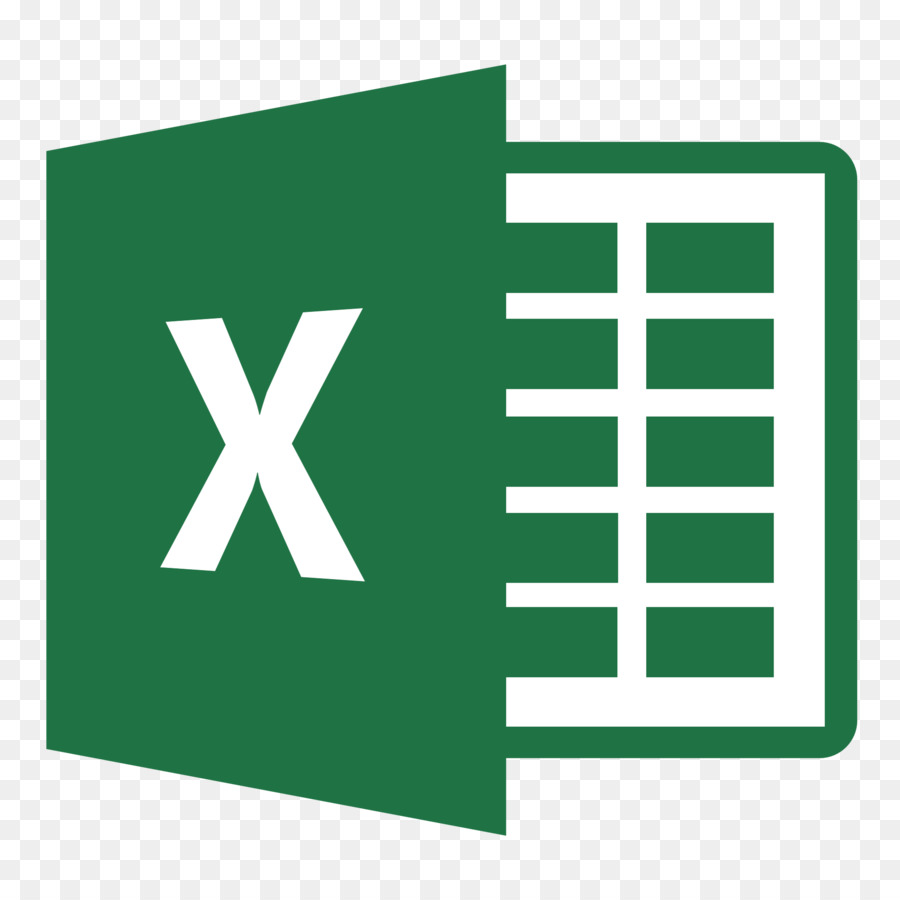
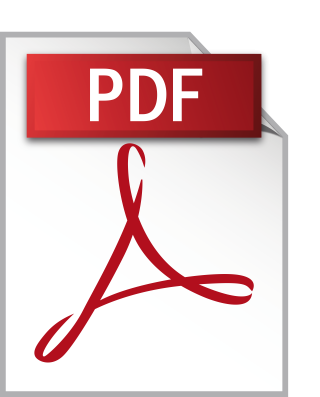
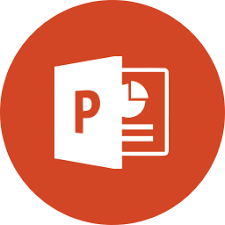
Metallographic cold mounting consumables are materials used to embed and protect specimens for microscopic analysis without using heat or pressure. These consumables involve liquid resins that harden at room temperature, preserving the structure of delicate, heat-sensitive, or irregularly shaped samples. They are commonly used for preparing samples that cannot withstand high temperatures, ensuring accurate examination and analysis.
The metallographic cold mounting consumables market is driven by the rising demand for precise material analysis across industries like automotive, aerospace, and electronics. Increasing adoption of automated sample preparation systems and advanced material research is fueling market growth. Challenges include maintaining high-quality standards while developing eco-friendly and low-toxicity products. Opportunities lie in creating specialized mounting solutions for complex materials and developing sustainable, fast-curing consumables compatible with automated processes.
The increasing demand for precise material analysis across industries is driving the growth of the metallographic cold mounting consumables market. Industries such as automotive, aerospace, electronics, and medical devices require detailed examination of material microstructures to ensure product reliability and compliance with safety standards. Cold mounting is preferred for delicate or heat-sensitive samples because it allows specimens to be preserved without exposure to high temperatures. As manufacturers work with advanced materials like composites and lightweight alloys, the need for accurate sample preparation using cold mounting techniques continues to grow. This demand is further supported by the expansion of quality control processes, where consistent and reproducible sample preparation is essential for detecting material defects and ensuring performance standards.
The growing adoption of automated and advanced testing technologies is contributing to the increased use of metallographic cold mounting consumables. Laboratories and industrial facilities are implementing automated sample preparation systems to improve efficiency and maintain consistency in sample analysis. Cold mounting materials, including epoxy resins and acrylic-based compounds, are used in these systems because they provide strong adhesion and minimize sample distortion. The rise in automated processes encourages the development of faster-curing and user-friendly cold mounting materials that integrate seamlessly with modern equipment. This technological shift enables higher throughput in testing processes while maintaining the precision required for advanced material investigations.
The rising investment in research and development activities across multiple industries is also accelerating the demand for metallographic cold mounting consumables. Material scientists and researchers rely on cold mounting techniques to analyze innovative materials and investigate their structural properties under various conditions. The need to understand new material behaviors in applications such as renewable energy, electronics, and biomedicine drives the use of specialized cold mounting solutions that preserve fine structural details. As governments and private sectors invest in advanced material research, the demand for cold mounting consumables that meet specific research needs is increasing, fostering market growth.
The focus on environmental sustainability and the need for safer laboratory practices are influencing the development and adoption of eco-friendly cold mounting consumables. Industries are seeking low-toxicity and biodegradable mounting materials to reduce environmental impact while maintaining high performance. Manufacturers are responding by creating products with reduced volatile organic compounds (VOCs) and improved safety profiles for users. This shift toward sustainable solutions aligns with global environmental regulations and corporate sustainability goals, further driving innovation and adoption of advanced cold mounting consumables.
The global metallographic cold mounting consumables market faces several challenges that affect its growth and adoption. The high cost of advanced cold mounting resins, especially epoxy-based materials, increases overall sample preparation expenses, which can limit their use among cost-sensitive industries. Variability in curing times poses operational difficulties, as longer curing periods delay the preparation process and reduce workflow efficiency. Ensuring consistent quality and adhesion across diverse specimen materials is complex, as different samples require specific formulations to achieve optimal results. Environmental and safety concerns related to the use of chemical resins present additional hurdles, with stringent regulations requiring manufacturers to develop low-toxicity and eco-friendly alternatives. Competition from hot mounting techniques, which are faster and more cost-effective for certain applications, also pressures the market. Limited awareness and technical expertise in emerging regions restrict market penetration, as specialized knowledge is required to select the right consumables and maintain accurate sample integrity. Supply chain disruptions and fluctuations in raw material availability further challenge manufacturers, leading to inconsistent product supply and increased production costs.
The increasing demand for eco-friendly and low-toxicity cold mounting consumables presents a significant opportunity in the metallographic cold mounting consumables market. As industries face stricter environmental regulations and prioritize sustainable practices, there is a growing need for mounting materials that minimize hazardous emissions while maintaining high performance. Developing biodegradable or low-volatile organic compound (VOC) formulations can meet these demands and attract customers seeking safer and more sustainable solutions. The advancement of specialized cold mounting consumables for complex and emerging materials also creates new opportunities. As industries such as renewable energy, aerospace, and medical devices adopt innovative materials like composites, ceramics, and advanced polymers, there is a rising need for mounting products capable of preserving delicate structures without distortion. This creates space for manufacturers to develop customized mounting solutions tailored to the unique characteristics of these materials. The increasing adoption of automated sample preparation systems in laboratories and industrial facilities offers further opportunities. There is a demand for cold mounting consumables compatible with these automated systems that provide faster curing times, improved handling, and consistent results. Companies that produce user-friendly, quick-setting, and reliable cold mounting products can gain a competitive edge as automated processes become more widespread. Expanding research and development in material science also provides growth potential for cold mounting consumables. As researchers explore new alloys, biomaterials, and nanostructures, there is a need for advanced mounting solutions that preserve the smallest details and maintain structural integrity under microscopic analysis. This growing focus on cutting-edge materials and new technologies offers long-term market opportunities for specialized and high-performance cold mounting products.
Product Type
Epoxy is the dominating segment in the metallographic cold mounting consumables market due to its superior mechanical properties, low shrinkage, and excellent adhesion to a wide range of materials. It is widely used for applications requiring precise specimen preparation and high-quality sample protection. Epoxy resins offer strong chemical resistance and are suitable for complex and delicate samples. Although curing times are longer compared to other resins, their durability and ability to provide clear, bubble-free mounts make them the preferred choice for industries requiring highly accurate analysis.
Acrylic resin is the fastest-growing segment in the metallographic cold mounting consumables market due to its quick curing time and ease of use. It is preferred in applications where fast sample preparation is required without compromising quality. Acrylic resins are known for their versatility, providing a balance between performance and efficiency. They offer moderate mechanical strength and are suitable for routine inspections and general-purpose mounting. Their ability to cure rapidly at room temperature makes them ideal for high-throughput environments where time efficiency is critical.
Polyester resin is used in the metallographic cold mounting consumables market for basic applications where cost efficiency is prioritized over advanced performance. It is typically used for non-critical sample preparation due to its lower mechanical strength and higher shrinkage compared to epoxy and acrylic resins. Polyester resins are easy to handle and provide a smooth surface finish but are less durable under demanding testing conditions. They are suitable for laboratories with low-volume mounting needs and where advanced material properties are not required.
The others category in the metallographic cold mounting consumables market includes specialized and hybrid resins tailored for specific applications. This segment covers materials designed to meet unique specimen requirements, such as improved thermal stability, enhanced transparency, or specialized hardness. These resins are used in niche applications where standard epoxy, acrylic, or polyester resins may not provide the required properties. While this segment is smaller, it continues to grow as new materials are developed to address specialized industrial and research needs.
Application
In the industrial specimen preparation segment of the metallographic cold mounting consumables market, there is a strong demand for materials that provide reliable encapsulation and preservation of samples. Industries such as automotive, aerospace, and electronics rely on accurate material analysis to ensure product quality and compliance with industry standards. Cold mounting consumables are widely used because they are effective for encapsulating delicate or heat-sensitive materials without causing damage. These consumables allow for the preparation of irregularly shaped or fragile samples, enabling precise cross-sectional analysis. As industrial manufacturing processes become more advanced, there is an increasing need for mounting products that offer fast curing times, improved mechanical stability, and compatibility with automated preparation systems to support large-scale testing and inspection.
In the metallographic research segment of the metallographic cold mounting consumables market, there is growing use of advanced mounting materials to support the study of complex materials and microstructures. Research laboratories in academic institutions, government agencies, and private organizations rely on cold mounting for detailed examination of innovative materials, including advanced alloys, ceramics, polymers, and composites. This segment demands mounting consumables that provide high transparency, chemical resistance, and dimensional stability to facilitate accurate microscopic and structural analysis. The ongoing development of new materials in sectors like renewable energy, medical devices, and nanotechnology is driving the need for specialized mounting solutions tailored to the unique characteristics of these emerging materials. Cold mounting consumables that offer superior edge retention and minimal shrinkage are crucial for maintaining the accuracy and reliability of research findings.
North America is a major market for metallographic cold mounting consumables due to the strong presence of industries like aerospace, automotive, and electronics that require precise material analysis. The region's focus on advanced manufacturing techniques and quality control drives the demand for high-performance cold mounting resins. Growth is supported by ongoing technological advancements and the need for accurate specimen preparation in research and industrial applications. However, the market faces challenges from rising costs of raw materials and stringent environmental regulations that push companies to adopt eco-friendly and low-toxicity products. Competitive pressure is strong, with companies focusing on innovation and offering customized solutions to meet diverse industry needs.
Europe holds a significant share of the metallographic cold mounting consumables market, supported by a well-established industrial base and stringent quality standards across sectors such as automotive, medical devices, and metallurgy. The growing emphasis on material testing for safety and compliance regulations drives market growth. Increasing investments in research and development to improve product performance and sustainability play a key role in shaping the market. Challenges arise from strict environmental regulations regarding the use of chemical resins, prompting manufacturers to develop sustainable and less hazardous alternatives. The competitive landscape is marked by the presence of both established players and emerging local manufacturers focused on specialized solutions.
The Asia Pacific region is the fastest-growing market for metallographic cold mounting consumables, fueled by rapid industrialization and the expansion of key sectors such as electronics, automotive, and heavy machinery. The region benefits from increasing research activities and the adoption of advanced manufacturing techniques, particularly in countries like China, Japan, and South Korea. Growing investments in quality assurance and materials testing further drive demand. However, the market faces challenges related to price sensitivity and inconsistent quality control practices in some areas. Companies are focusing on improving product affordability while maintaining performance standards to cater to the diverse needs of industries across the region.
Latin America shows steady growth in the metallographic cold mounting consumables market, mainly driven by the automotive and mining industries. Rising industrial activities and increasing awareness of the importance of precise material analysis contribute to market expansion. However, limited technological adoption and the high cost of specialized consumables restrict wider use. Supply chain inefficiencies and the dependence on imports also create challenges for market players. Companies operating in the region are focusing on providing cost-effective solutions and improving local distribution networks to overcome these barriers and enhance market reach.
The Middle East & Africa market for metallographic cold mounting consumables is relatively small but growing due to increased industrial activities in sectors like oil and gas, construction, and mining. The demand for reliable material testing and quality control is rising as industries seek to comply with international standards. However, the market faces challenges from a lack of technical expertise and limited local manufacturing capabilities. High import costs and logistical constraints further impact market growth. Companies are investing in training programs and expanding their regional presence to meet the growing demand and improve customer support in this emerging market.