High Rigidity Cutting Tool Market
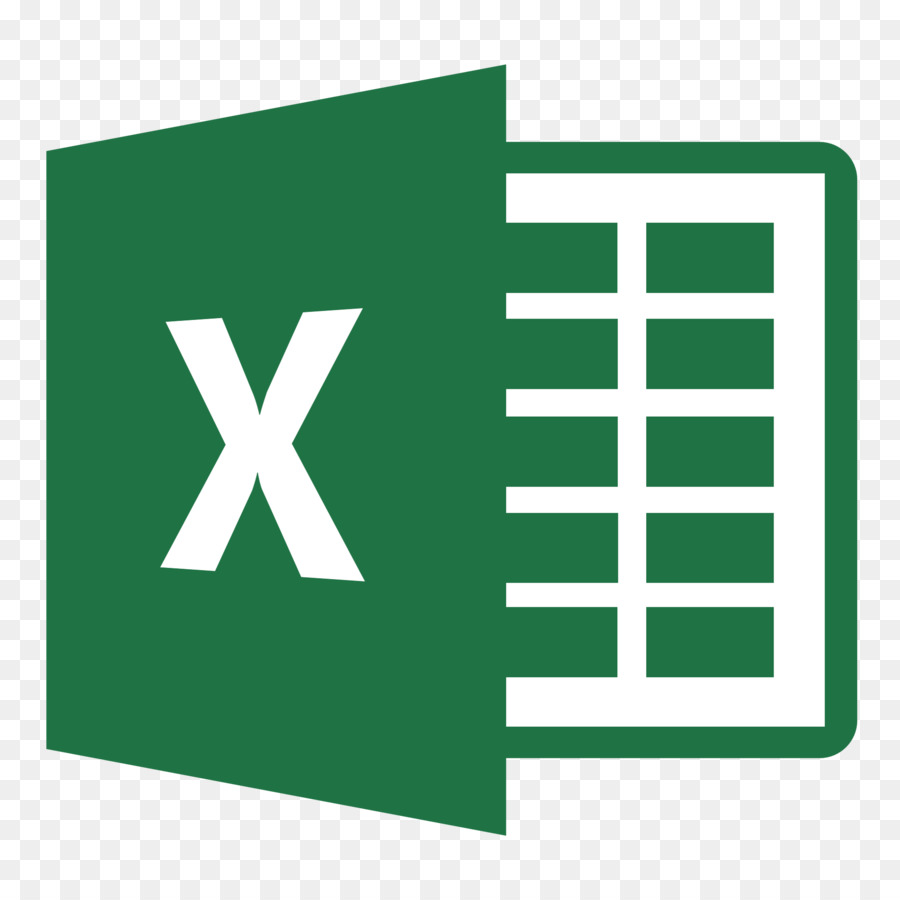
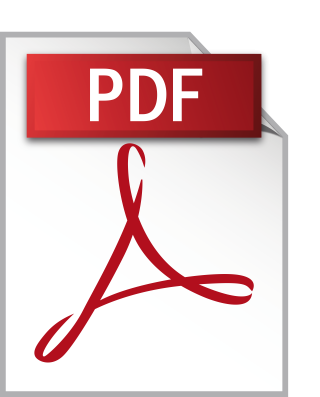
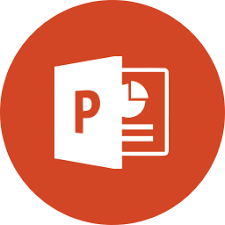
A high rigidity cutting tool is designed to withstand high cutting forces, providing enhanced stability and precision during machining operations. These tools are typically made from materials like carbide or high-speed steel, which offer superior strength and wear resistance. High rigidity helps reduce tool deflection, vibration, and chatter, resulting in improved surface finishes and longer tool life.
The high rigidity cutting tool market is driven by the increasing demand for precision and efficiency in industries such as automotive, aerospace, and manufacturing. However, the high cost of advanced materials and complex manufacturing processes presents a challenge for widespread adoption, especially among small and medium-sized manufacturers. Opportunities in the market arise from the growing trend of automation and Industry 4.0, which creates a need for tools that can maintain performance in automated production environments. Additionally, advancements in materials and manufacturing technologies present avenues for innovation and market growth.
The global high rigidity cutting tool market is primarily driven by the increasing demand for precision engineering across various industries such as automotive, aerospace, and manufacturing. As manufacturing processes require more accuracy and quality in their products, the need for high rigidity cutting tools grows. These tools provide the necessary stability and precision, ensuring high-quality finishes and minimizing defects in production. This demand for high-precision components in industries such as aerospace and automotive, where tight tolerances are crucial, has led to a significant rise in the adoption of high rigidity cutting tools.
Advancements in materials and manufacturing technologies also play a significant role in expanding the market. The development of new materials like carbide and ceramic-based cutting tools, which offer enhanced hardness and wear resistance, has fueled the growth of the high rigidity cutting tool market. These materials allow tools to maintain their integrity under extreme machining conditions, providing greater reliability and performance. Moreover, the continuous evolution of computer numerical control (CNC) machining and other advanced manufacturing processes has created a need for cutting tools that can handle high-speed operations and maintain stability over long production cycles.
Economic growth, particularly in emerging markets, has also contributed to the demand for high rigidity cutting tools. As industries in countries such as China, India, and Southeast Asia continue to expand and modernize their manufacturing sectors, the need for more efficient and durable cutting tools has risen. These markets are increasingly adopting advanced machining technologies, which in turn increases the demand for high rigidity tools that can support complex and high-speed operations.
Environmental regulations and the push for sustainability are influencing the design and development of cutting tools as well. Manufacturers are under pressure to improve energy efficiency and reduce material wastage in their operations. High rigidity cutting tools help achieve these goals by enabling faster and more efficient machining, which reduces energy consumption and minimizes waste. This shift towards environmentally friendly production processes is driving the adoption of these tools in various industrial sectors.
The high rigidity cutting tool market faces challenges related to the high cost of advanced materials and manufacturing processes. Cutting tools made from high-performance materials such as carbide, ceramics, and cermet are expensive to produce, which increases the overall cost of the tools. This can be a barrier for small and medium-sized manufacturers who may not have the capital to invest in such tools. Moreover, the complex and precision-based production methods required to manufacture these cutting tools add to their cost. While the tools offer long-term durability and high performance, their upfront price can limit their widespread adoption, particularly in cost-sensitive industries.
The global high rigidity cutting tool market presents opportunities in the growing trend of automation and Industry 4.0. As manufacturing industries continue to integrate automation and smart manufacturing systems, there is an increasing demand for cutting tools that can operate seamlessly within these advanced production environments. High rigidity cutting tools are well-suited for automated systems, as their precision and durability enhance the overall efficiency of automated machining processes. This shift towards automation creates opportunities for manufacturers of high rigidity cutting tools to develop specialized products that meet the specific needs of automated production lines, such as tools designed for high-speed, high-precision applications in robotics and automated assembly systems. As these technologies evolve, the demand for cutting tools capable of handling complex and high-volume operations will continue to grow, opening new markets for manufacturers in the cutting tool industry.
In North America, the high rigidity cutting tool market is driven by advanced manufacturing industries such as aerospace, automotive, and medical devices. The region's strong focus on precision engineering and high-quality production standards creates a steady demand for cutting tools that offer superior rigidity and durability. The adoption of new technologies, including CNC machining and automation, is also boosting the need for high-performance cutting tools. Moreover, the ongoing trend toward reshoring manufacturing activities to the U.S. has further increased the demand for advanced machining tools, contributing to the growth of the high rigidity cutting tool market in this region.
Europe, with its highly developed automotive, aerospace, and industrial machinery sectors, presents a significant market for high rigidity cutting tools. Countries like Germany, Italy, and France are key players in the manufacturing of high-precision machinery and components, where the need for cutting tools that can provide high stability and precision is essential. The European market is also influenced by the strong emphasis on sustainability and energy efficiency, encouraging manufacturers to adopt advanced tools that enhance machining efficiency and reduce material waste. The push for innovation and research in materials science is likely to support market growth in this region.
In Asia Pacific, the market for high rigidity cutting tools is experiencing rapid growth due to the booming manufacturing sector in countries like China, Japan, and India. The region’s increasing industrialization, particularly in automotive, electronics, and heavy machinery manufacturing, is creating a robust demand for cutting tools with higher performance capabilities. The rapid adoption of automation and smart manufacturing technologies in countries like China and Japan is further fueling the market growth, as these technologies require precise, durable tools that can perform consistently at high speeds. Moreover, as more manufacturers in the region seek to upgrade their machining capabilities, the demand for high rigidity cutting tools continues to rise.
Latin America’s high rigidity cutting tool market is comparatively smaller but shows potential for growth, driven by the expanding automotive and manufacturing sectors in countries like Brazil and Mexico. The increasing focus on local manufacturing capabilities and the demand for more efficient production processes in the region contribute to the need for high-performance cutting tools. However, economic challenges, including fluctuating currency values and political instability, may affect the pace of market growth in this region.
In the Middle East and Africa, the market for high rigidity cutting tools is relatively underdeveloped but presents emerging opportunities, particularly in the oil and gas, mining, and construction sectors. Countries like Saudi Arabia, the UAE, and South Africa are investing heavily in infrastructure and industrialization projects, creating a need for advanced cutting tools that can handle demanding conditions and high-performance requirements. While the market is still evolving, the region’s growing industrial base and infrastructure development projects are expected to contribute to the expansion of the high rigidity cutting tool market in the coming years.