Heavy Payload Cobots Market
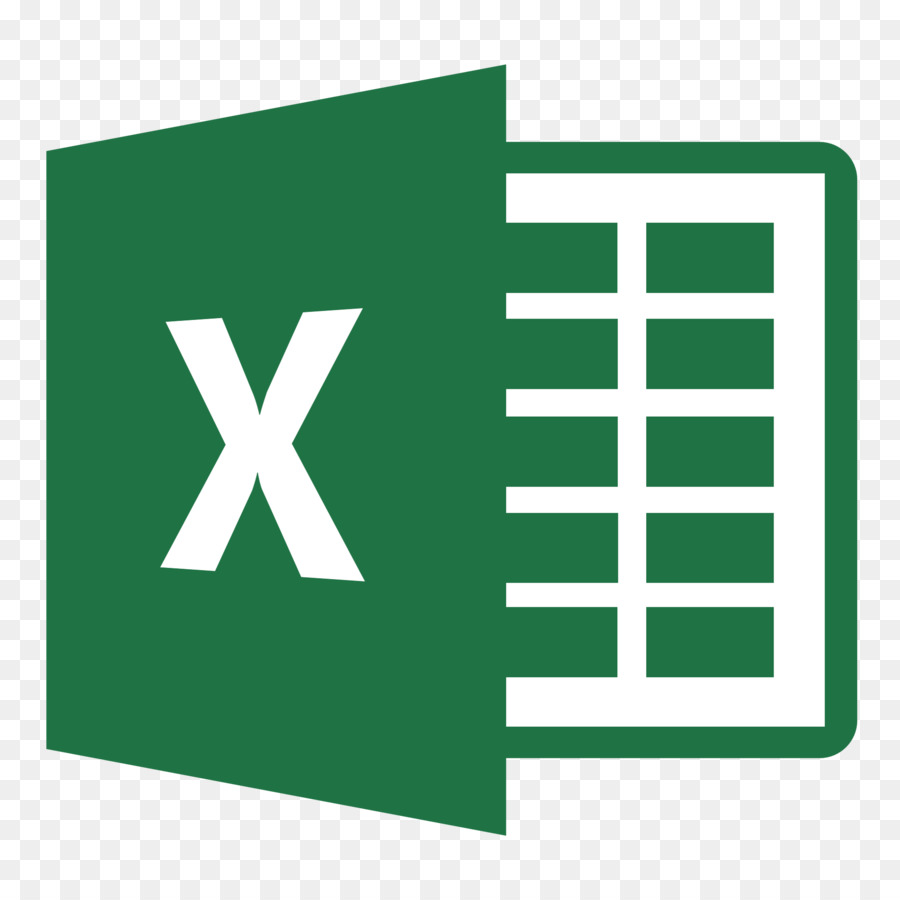
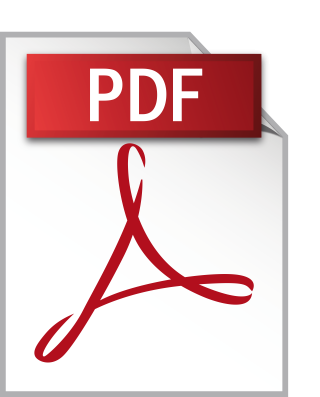
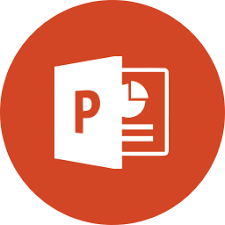
Heavy payload cobots are collaborative robots designed to handle and lift significantly heavy loads while working alongside human operators. These advanced robots combine strength and precision, enabling industries to safely automate tasks involving bulky or heavy items, enhancing productivity and reducing physical strain on workers.
The heavy payload cobots market is driven by the increasing need for automation in industries requiring the handling of heavy loads, boosting productivity and enhancing worker safety. Challenges such as high initial costs, integration complexities, and technical limitations impact adoption, particularly for smaller enterprises. However, opportunities arise from technological advancements in AI and robotics, which improve the versatility and efficiency of these cobots. The shortage of skilled labor and the push for sustainable practices further encourage the growth of the market as businesses seek solutions to optimize operations and reduce costs.
The global heavy payload cobots market is driven by several compelling factors. One of the primary drivers is the increasing need for automation in industries requiring the handling of heavy goods, such as automotive, manufacturing, and logistics. These industries benefit from cobots' ability to enhance efficiency, reduce operational costs, and improve safety by taking on physically demanding tasks that would otherwise put workers at risk. The ability of cobots to work collaboratively with human operators without the need for extensive safety barriers helps create a flexible and integrated workspace.
Advancements in technology have also fueled the growth of the heavy payload cobots market. Improved sensors, machine learning, and AI integration have made these robots more sophisticated, allowing them to handle complex tasks with precision. This technological evolution ensures that heavy payload cobots can operate with greater adaptability and can be programmed for various applications, leading to increased adoption across sectors. The combination of enhanced safety features and high payload capacity has made these robots a valuable addition to production lines where repetitive or hazardous tasks are common.
The growing emphasis on worker safety and ergonomic improvements is another significant factor pushing the demand for heavy payload cobots. With a focus on minimizing workplace injuries and improving the well-being of employees, companies are turning to cobots to take on strenuous lifting and repetitive handling tasks. This not only minimizes the risk of injuries but also supports the workforce by reallocating human labor to more strategic and less physically demanding roles.
Regulatory standards and policies aimed at promoting safer working environments also play a crucial role in the market expansion. Governments and industry bodies are increasingly endorsing automation solutions that prioritize both productivity and employee safety. These regulations encourage industries to adopt safer alternatives to traditional industrial robots, making heavy payload cobots an attractive solution.
The labor shortage in many advanced economies is another compelling driver for the heavy payload cobots market. With a shrinking pool of skilled labor and increasing operational demands, companies are investing in robotics to fill gaps in their workforce. Cobots are particularly appealing due to their ability to assist or even replace human workers in high-demand environments without the steep training requirements that conventional industrial robots might entail. This shift supports continuous production while addressing the shortage of manual labor.
One of the significant challenges facing the global heavy payload cobots market is the high initial investment required for deployment. While cobots offer long-term cost savings through increased productivity and reduced labor expenses, the upfront costs can be a barrier for small and medium-sized enterprises (SMEs) with limited budgets. The price of advanced cobot systems, which includes the cost of hardware, software, and integration, may deter companies from adopting this technology, slowing market growth in certain sectors.
Another challenge stems from the technical complexities associated with integrating heavy payload cobots into existing production lines. Companies often face difficulties when adapting their current systems to work seamlessly with new robotic technologies. This can involve extensive recalibration, reprogramming, and training, which can lead to disruptions in production. Companies may also need to upgrade their infrastructure to fully support the integration of cobots, adding to the complexity and overall cost of adoption.
The development of standardized protocols for safety and interoperability is still a work in progress. The absence of universal standards for heavy payload cobots means that companies may have to navigate different guidelines and compliance requirements when deploying these robots in multiple regions or industries. This inconsistency can make it difficult for businesses to scale their use of cobots efficiently and can lead to additional regulatory hurdles and potential delays.
There is also a challenge in addressing the technical limitations and reliability of heavy payload cobots, particularly when it comes to operating in harsh environments or dealing with highly variable payloads. Cobots, although capable of handling significant weight, may still face difficulties with durability and operational consistency in challenging conditions, such as extreme temperatures, dusty areas, or environments that require precise handling of irregularly shaped objects. This can limit their application in certain industries, such as heavy manufacturing and construction, where environmental factors are more extreme.
Another factor impacting the market is the shortage of skilled professionals who can design, program, and maintain heavy payload cobots. The implementation and upkeep of robotic systems require specialized knowledge and technical expertise, which may not be readily available in many regions. This skills gap can slow down the adoption of heavy payload cobots as companies may struggle to find qualified personnel or invest in extensive training programs to upskill their workforce. This challenge can create a barrier to scaling operations and optimizing the use of cobots within a company's production ecosystem.
The global heavy payload cobots market presents significant opportunities due to the increasing demand for enhanced productivity and safety in industries like automotive, manufacturing, and logistics. Companies are recognizing the potential of heavy payload cobots to automate tasks that involve lifting, transporting, and assembling large items, leading to higher operational efficiency and reduced human strain. The continuous advancements in robotics and AI are enabling these cobots to become more adaptable and capable of performing complex tasks with precision, creating opportunities for their adoption in a wider range of applications. The integration of cobots with the Internet of Things (IoT) and smart factory systems further expands their functionality, making them an attractive solution for industries aiming to implement Industry 4.0 practices. Additionally, as the global workforce faces a shortage of skilled labor, heavy payload cobots offer a viable solution to fill the gap by taking on repetitive, physically demanding roles and allowing human employees to focus on more strategic tasks. This shift not only ensures continuity in production but also supports workforce safety and overall job satisfaction. The growing emphasis on sustainable and eco-friendly practices provides further opportunity, as cobots can be used to optimize processes, reduce waste, and lower energy consumption. With governments and organizations increasingly supporting automation through incentives and grants, companies are encouraged to invest in these technologies, boosting growth opportunities in the market.
The North American market for heavy payload cobots is driven by technological innovation and significant investments in automation across key industries such as automotive, manufacturing, and logistics. The region's strong emphasis on enhancing productivity, safety, and operational efficiency has fueled the adoption of collaborative robotics. The U.S. leads this market due to its advanced industrial sector, supported by ongoing research and development initiatives and government policies that encourage automation and smart manufacturing. High labor costs and the need to address worker safety also contribute to the growth of heavy payload cobots, as companies seek solutions to maintain competitive advantages.
In Europe, the heavy payload cobots market benefits from a combination of robust industrial infrastructure and strong regulatory support. Countries like Germany, the U.K., and France are at the forefront of adopting cobot technology, driven by the push towards Industry 4.0 and digital transformation strategies. European industries are particularly focused on improving workplace safety and reducing manual labor, making cobots an attractive solution. The region's emphasis on sustainability and environmental regulations further supports the use of advanced, energy-efficient robotic systems. Collaboration between governments and private sectors through funding and innovation grants has also accelerated the growth of automation, including heavy payload cobots.
Asia Pacific is witnessing the fastest growth in the heavy payload cobots market, primarily due to rapid industrialization, large-scale manufacturing, and the push for increased automation in countries such as China, Japan, and South Korea. China’s emphasis on becoming a global leader in manufacturing and technology has led to significant investments in robotics and automation solutions. The region's adoption of heavy payload cobots is driven by labor shortages, rising wages, and the need for higher production capacities. The availability of cost-effective manufacturing and a robust supply chain ecosystem further support the expansion of the market. Additionally, countries like Japan and South Korea have a history of embracing cutting-edge technology, and their industries are now looking at cobots as a way to bolster productivity and maintain economic growth.
In Latin America, the heavy payload cobots market is evolving, with Brazil and Mexico being the primary drivers. While the region has been slower to adopt automation compared to North America and Europe, there is a growing awareness of the benefits that cobots can bring to industries such as automotive, food and beverage, and manufacturing. The economic challenges and a workforce that is increasingly open to technological advancements have pushed companies to explore solutions that offer efficiency and cost savings. However, the market is hindered by economic instability and the relatively high costs of advanced robotics, making gradual adoption more likely.
The Middle East & Africa market for heavy payload cobots is still in its nascent stage, but it holds potential due to the region's ongoing investments in industrial development and modernization. Countries like the United Arab Emirates and Saudi Arabia are taking significant steps toward diversifying their economies, which includes adopting advanced automation technologies to boost productivity in sectors such as oil and gas, manufacturing, and logistics. However, the region faces challenges such as a lack of skilled labor to operate and maintain such advanced technologies and the need for significant capital investment. The market is expected to grow as infrastructure improves and governments continue to push for economic diversification and innovation through various incentive programs.