Fabricated Tubes Market
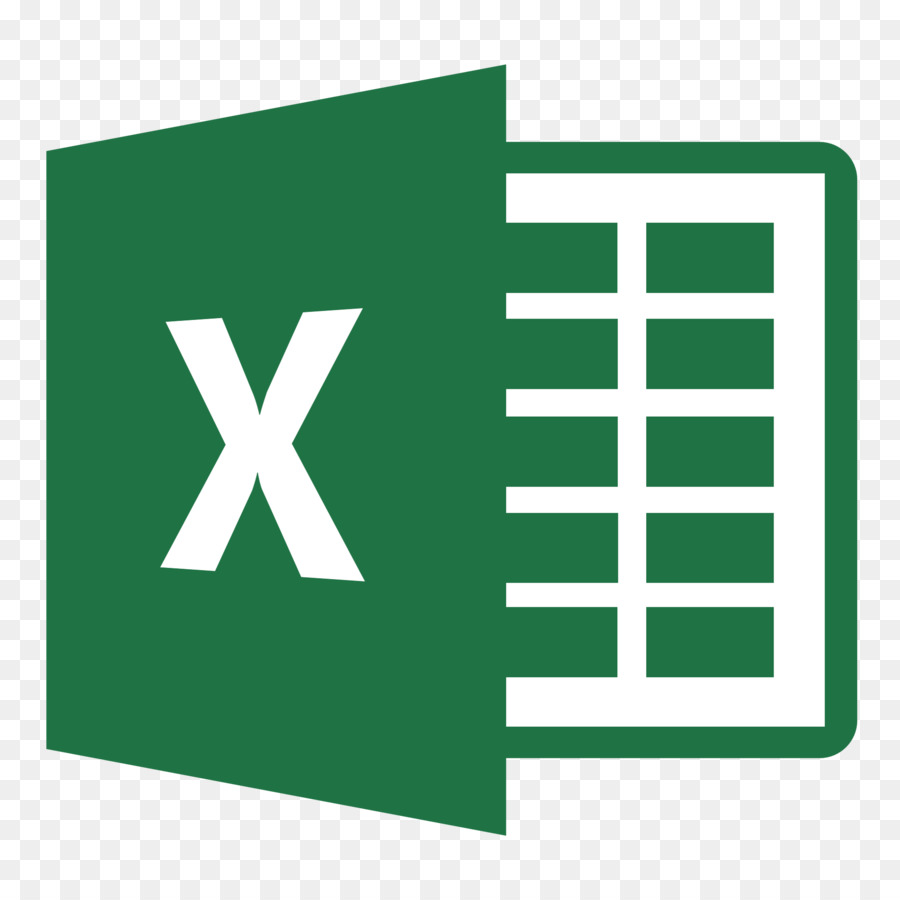
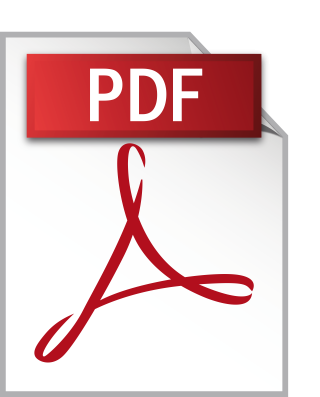
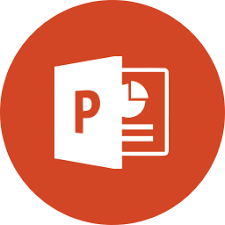
Fabricated tubes are customized tubular structures designed and manufactured to meet specific requirements across industries. These tubes undergo processes like cutting, bending, welding, and finishing to achieve desired shapes, sizes, and functionalities, making them suitable for applications in automotive, construction, aerospace, and industrial equipment.
The fabricated tubes market is driven by increasing demand across industries such as automotive, construction, and renewable energy, where customized and high-performance materials are essential. However, challenges like fluctuating raw material prices, complex manufacturing processes, and stringent regulatory requirements can impact market growth. Opportunities lie in the rising need for lightweight, sustainable materials, advancements in manufacturing technologies, and the growing focus on renewable energy and infrastructure development.
The global fabricated tubes market is driven by the increasing demand for customized components across a wide range of industries. As industries like automotive, construction, and aerospace continue to evolve, there is a growing need for precision-engineered tubes that meet specific performance standards, including strength, durability, and flexibility. The ability of fabricated tubes to be tailored to various shapes and sizes, making them ideal for complex applications, has become a crucial factor driving their adoption.
The expansion of infrastructure development and urbanization across emerging economies has also played a significant role in boosting the demand for fabricated tubes. These tubes are widely used in construction projects for structural support, plumbing, and electrical systems, leading to their growing presence in building and infrastructure developments. As these economies invest in modernizing their infrastructure, the need for high-quality, reliable fabricated tubes continues to rise.
Technological advancements in manufacturing processes, such as automated fabrication and advanced welding techniques, have made the production of fabricated tubes more cost-effective and efficient. These innovations enable manufacturers to produce tubes with greater precision, strength, and consistency, further fueling the market's growth. As industries seek to improve operational efficiency and reduce costs, fabricated tubes offer a reliable and high-performance solution to meet their needs.
The rising focus on sustainability and environmental concerns also contributes to the growth of the fabricated tubes market. With an increasing emphasis on eco-friendly construction practices and energy-efficient designs, fabricated tubes, particularly those made from recyclable or energy-efficient materials, are in demand. Their use in renewable energy projects, such as wind turbines and solar installations, adds another layer of opportunity in the market.
The global fabricated tubes market faces challenges related to the fluctuating prices of raw materials, such as steel and alloys, which directly impact production costs. Volatility in raw material prices can create financial uncertainties for manufacturers, leading to price instability and supply chain disruptions. Moreover, the complexity of producing customized tubes with precise specifications requires advanced technology and skilled labor, which can increase manufacturing costs and limit production scalability. The market also faces stringent regulatory requirements for material quality, environmental standards, and safety, which demand continuous compliance and investment in quality control measures. These factors combined can create challenges in maintaining profitability and competitive pricing in the market.
The global fabricated tubes market presents opportunities in the growing demand for lightweight and high-performance materials, particularly in industries like automotive and aerospace. As these sectors prioritize fuel efficiency and improved performance, there is an increasing need for fabricated tubes made from advanced, lightweight materials that maintain strength and durability. This demand for specialized materials opens up avenues for innovation in fabrication techniques and the development of new alloys and composites.
The expansion of renewable energy projects, including wind and solar power, creates opportunities for fabricated tubes to be used in the construction of energy-efficient and sustainable infrastructure. With the growing focus on green energy, the demand for fabricated tubes in the manufacturing of renewable energy systems, such as wind turbine components and solar panel frames, is on the rise. This trend offers a significant opportunity for market players to cater to a rapidly expanding industry that aligns with global sustainability goals.
As industries increasingly focus on automation and smart manufacturing, the use of fabricated tubes in advanced machinery and robotics is expected to grow. Automated production processes require precision-engineered tubes that can withstand high stress and perform under demanding conditions. The integration of IoT (Internet of Things) and sensor technologies in industrial applications also presents a new market for fabricated tubes that are compatible with modern, tech-driven systems.
The demand for customization and tailored solutions in various sectors provides another growth opportunity for the fabricated tubes market. With industries looking for components that meet specific needs, such as unique shapes, sizes, or enhanced properties, manufacturers can capitalize on offering bespoke fabrication services. This trend is particularly relevant in sectors like construction, where structural components require exact specifications to ensure safety and performance.
Product Type
The copper segment in the fabricated tubes market is widely used due to copper’s excellent thermal and electrical conductivity, making it essential for applications in electrical systems, heat exchangers, and plumbing. Copper tubes are also valued for their corrosion resistance and high strength, particularly in environments where durability is crucial, such as in the automotive and aerospace industries. This segment benefits from copper’s versatility and reliability in various industrial and commercial applications.
The aluminum segment is gaining traction in the fabricated tubes market due to the metal’s lightweight nature, corrosion resistance, and ability to be easily fabricated into different shapes. Aluminum tubes are extensively used in sectors like construction, automotive, and transportation, where the reduction of weight without compromising on strength is a critical requirement. The demand for energy-efficient materials in industries such as aerospace and renewable energy further supports the growth of aluminum tubes.
The others segment includes various metals and alloys such as stainless steel, brass, and titanium, each offering specific properties suited to specialized applications. Stainless steel tubes are highly sought after in industries like food processing, pharmaceuticals, and chemical manufacturing due to their resistance to corrosion, high temperature tolerance, and strength. Brass and titanium tubes, with their unique combination of properties, cater to niche applications in industries such as medical devices, marine engineering, and specialized machinery.
Application
The industrial segment of the fabricated tubes market is driven by demand across various sectors, including construction, automotive, and energy. These tubes are widely used in heavy-duty applications, such as structural support, machinery, and energy systems. Their durability, strength, and versatility make them ideal for industrial processes that require reliable and high-performance components to withstand harsh environments and heavy workloads.
The medical segment relies on fabricated tubes for their use in medical devices, surgical instruments, and healthcare systems. Materials like stainless steel and titanium are commonly used in the production of medical tubes due to their biocompatibility, resistance to corrosion, and ability to maintain precision. These tubes are essential for applications such as intravenous (IV) systems, catheters, and diagnostic equipment, where hygiene and performance are critical.
The manufacturing industry segment utilizes fabricated tubes in the production of machinery, vehicles, and equipment. Tubes in this sector are used for creating components that require specific strength and flexibility, such as piping systems, structural elements, and cooling systems. The customization of these tubes allows manufacturers to meet specific operational demands, leading to their widespread use in producing efficient, long-lasting machinery and industrial products.
The others segment encompasses a variety of specialized applications in sectors like aerospace, defense, and marine industries. These tubes are often made from high-performance materials like titanium and specialty alloys, which offer properties such as lightweight strength, corrosion resistance, and high-temperature tolerance. These tubes are crucial for building advanced technologies and systems used in transportation, energy, and national security.
In North America, the fabricated tubes market benefits from strong industrial and manufacturing sectors, particularly in the automotive, aerospace, and construction industries. The region's focus on innovation and high-quality production standards drives demand for precision-engineered tubes. Additionally, the increasing push for sustainable energy solutions, such as wind and solar energy, further boosts the demand for fabricated tubes in renewable energy projects.
Europe has a well-established manufacturing base, with countries like Germany, Italy, and the UK leading the demand for fabricated tubes in automotive, machinery, and construction applications. The region’s emphasis on environmental regulations and sustainability has also accelerated the use of advanced materials, creating opportunities for fabricated tubes in sectors focused on energy efficiency and green technologies. Europe's growing infrastructure projects, along with its strong presence in the aerospace industry, continue to support the market's expansion.
Asia Pacific is experiencing rapid industrialization and urbanization, contributing to the increasing demand for fabricated tubes. Major markets like China, Japan, and India are seeing significant growth in sectors such as automotive, construction, and energy, which require high-performance, customized tube solutions. The region's large manufacturing base and growing infrastructure developments provide vast opportunities for fabricated tube suppliers, especially as the demand for advanced and lightweight materials rises in these rapidly evolving industries.
In Latin America, the fabricated tubes market is primarily driven by the expansion of the automotive, mining, and oil and gas sectors. Countries like Brazil and Mexico are focusing on infrastructure development and industrial modernization, creating a growing demand for customized and durable tube solutions. The region’s natural resource industries, such as oil extraction, further boost the demand for fabricated tubes used in machinery and transportation.
The Middle East & Africa region sees demand for fabricated tubes largely driven by the oil, gas, and construction industries. The Middle East, in particular, is known for large-scale infrastructure projects, where fabricated tubes are essential for building structures and facilitating heavy lifting. The region’s significant investments in energy and infrastructure, as well as the increasing focus on sustainability, contribute to the growing demand for fabricated tube products designed to meet harsh environmental conditions. Africa, with its expanding mining and energy industries, also offers opportunities for fabricated tube suppliers to cater to the needs of these sectors.